From the initial concept to the logistics, we take care of every part of the process up to the last detail. We work hand in hand with the client and being manufacturers allows us customize orders.
Our team is organized into different working departments working collectively, which allows us to give effective solutions to the customer, whilst maintaining total control of each of the processes. This is our circle of value.
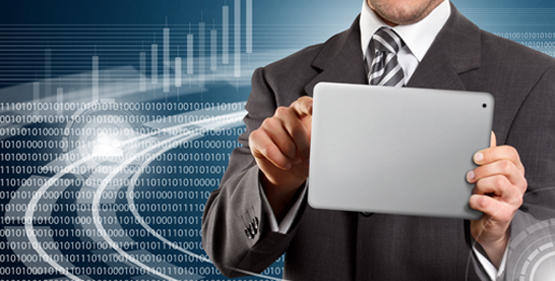
CONCEPT
Product and Process Engineering Departments work on the selection and development of the most competitive and efficient design and manufacturing concepts, in accordance with state of the art technologies.
CEFA support their customer in the earliest program stages, aligning strengths with their customers´ targets and expectations; shifting their engineering resources to customer’s Engineering Centres, if requested.
Design Cost Control System by CEFA allows defining the program at an affordable cost as well as its tracking and control during every program development phase.
CEFA Product and Process Engineering perform design control reviews throughout product lifetime to achieve targets of cost reductions programs to be shared with the customer.
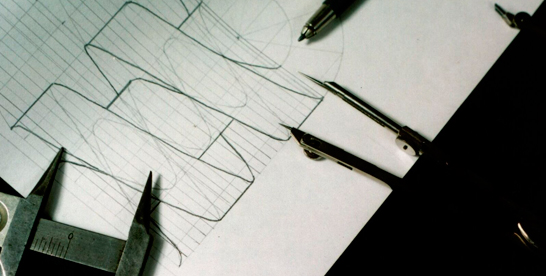
DESIGN
- Product Design and CAD Construction at customer Development and Engineering Centre, according to customer’s standards
- Program Management supported by tools for PLM, APQP Management and Economics Control
- Plant Staff Involvement in earliest development stages to guarantee Process Robustness and proper Design for Manufacturing
- Concept Validation by means of state of the art tools:
- CAE simulations in its different variants: Resistance Analysis by means of FEA, Computational Fluid Dynamics (CFD), Vibration and Rattling, Head Impact, Crash Simulation, Pedestrian protection…
- Rapid Prototyping.
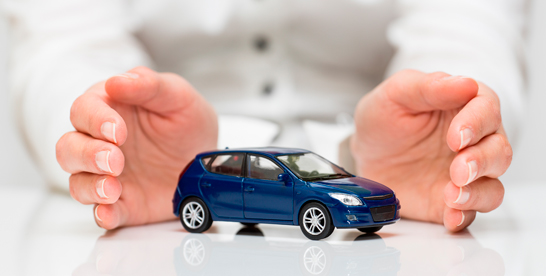
TESTING AND VALIDATION
Performance of functional trials and tests according to PRODUCT DESIGN AND VALIDATION PLAN, developed according to customer requirements (SOR).
- Control 3D by means of CCM (by means of contact or laser) or Digital Scanning
- DETERMINATION OF TECHNICAL POLYMERS’ PROPERTIES:
- Mechanical Tests ( Yield Stress, Flexural Modulus, Charpy impact strength..)
- Physical Tests ( Density, Melt Temperature, Ash Content…)
- Functional Tests (Vicat softening Temperature, Melt Flow Index….)
- FUNCTIONAL TEST OF SUPPLY PRODUCTS:
- Resistances ( Thermal resistance, Impact Strength, Strain at break….)
- Ageing and Durability ( Weather, Temperatures, Pressure Resistance, Vibrations…)
- Combine Tests of Temperature and Vibrations durability…
- APPEARANCE TESTS:
- o Scratch Test, Measure of Colour (Spectrophotometer)
- o Colour Fastness to Artificial Light Test
- Thermal Shock- Vibration Durability Test for expansion bottles, power steering reservoir tanks…
- Airbag Test on Instrument Panel at different temperatures (Environmental Tª, -35ºC, 85ºC…)
- Specific tools are built according to the requirement of new products development…
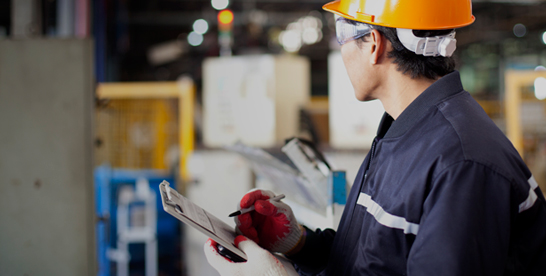
TOOLING
- Moulds manufacturing management.
- Tooling development and management involving fully committed and experienced suppliers.
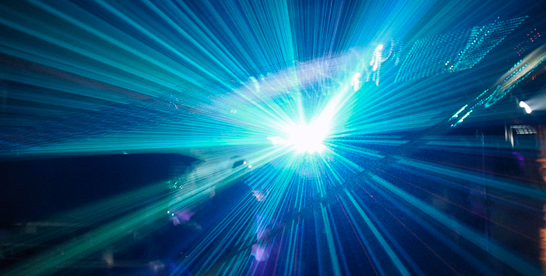
PRODUCTION
Following production technologies are available and supported by experienced technicians.
- Injection Moulding
- Standard
- Gas Assisted
- Two Components (2K)
- Insert moulding
- Low pressure Back Injection (fabrics, foils,..)
- Injection-Compression
- Thermoplastics Welding
- Hot Plate
- Infrared
- Ultrasonic
- Vibration
- Heat Staking
- Laser technologies
- Micro perforation
- Cutting
- Marking
- Other Technologies
- IMG, Painting, Flocking, Chrome Plating, Tampo printing,…
- Fully Automated Manufacturing Units
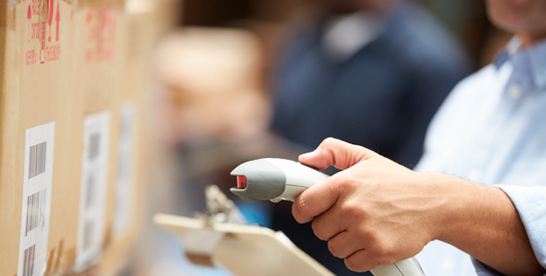
LOGISTIC
- Capacity for locating parts all over the world.
- EDI messages interchange.
- Management of sequecial and scheduled deliveries.
- Issue of documents following ODETTE norms.
- Optimised control of material flow, including methods such as KANBAN, Just in time deliveries and SILS.
- Purchasing management using MRP (SAP).
- Authomatic warehouse managent using bar code readers.
- Value add parts management.